OG212 Dual-Measure Tooke® Gage
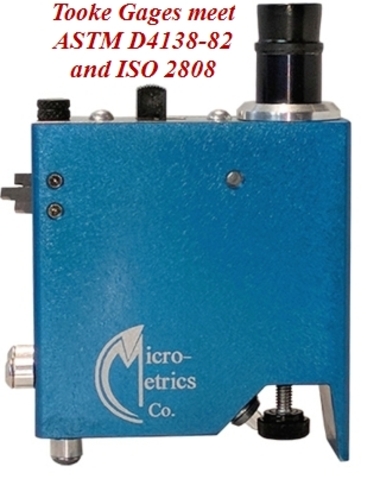
The OG212 Tooke Paint Inspection Gage is a precision tool for inspection and dry-film thickness measurement (in accordance with ASTM D4138) of single or multiple coats on any substrate, and for microscopic observation and measurement of substrate and film defects.
Dual-Measure features
- Dual-Measure scope, with 1 mil per hashmark space above the line and 20 microns per hashmark space below the line scale.
- Measures thickness of coatings applied to wood, plastic, cement, glass, ceramics, mirror backings, metal, etc.
- Assists in measuring brittleness and adhesion of coatings and materials.
- Both the OG212 and OG214 are supplied with 1✕, 2✕, and 10✕ cutting tips installed in the gauge body. An optional 5✕ cutting tip is available.
- Gauges come in a rugged plastic carrying case with cutting tip wrench, indelible marker, spare LED bulb, and spare batteries
![]() | ![]() |
The Tooke Gage uses an illuminated 50-power microscope equipped with the new Dual-Measure microscope with a measuring reticle marked in both mils and microns. The gage mounts three tungsten carbide cutting tips for precise incision of the work surface. Standard cutting tips are 1X, 2X, and 10X. (An optional 5X tip is available.) Also, a gauge can be ordered with any three tips desired, or with a single precision-ground tip and two blanks.
Oct 2019: Peter M., Product Quality Manager at a major industrial client:
The new reticles are AMAZING!
I have 2 more [gauges for scope swaps] in the mail for you and would like to purchase a new gauge as well.
FYI, I plan to purchase one more new one after this and will also send another 2 for new scopes after I get these back; that should take care of us.
Thanks again, these are AWESOME!
I can add that I took the Tooke to the line and watching my inspectors use the new gauge was like watching my kids at Christmas.
Direct measurement of total dry-film coating thickness and thickness of individual coats of paint is a unique capability of the Tooke Paint Inspection Gage. Thus, in addition to routine use, it often serves as a “referee” instrument to calibrate indirect or non-destructive thickness measuring instruments.
(Note: Each microscope is validated before sale against a certified gage block traceable to the National Institute of Standards & Technology (NIST). An OEM calibration certificate is available for an additional fee.)
Special applications
The Tooke Gage has been used to assess sandblast cleaning work, to measure plating and paint thickness on ceramics, metal, wood, and concrete, and even to measure protective backing thickness on mirrors. It is virtually the only tool for measuring paint on plastics. The quality of the incision in the film discloses much about the characteristics of the brittleness and adhesion of the material.
Other uses include assessment of substrate conditions and coating adhesion, and observation of microscopic cracking, tendency for brittleness, cratering, or other microscopic film symptoms.
Construction
The anodized Dual-Measure microscope reticle
is marked in mils and microns.
The aluminum gauge body contains an illuminated microscope and mounts three tungsten-carbide cutting tips (that incise the “V-groove” for measuring) on the narrow side. Two guide studs project from the body on the same side as the cutting tips. The tripod thus formed by the three legs (guide studs and cutting tip) provides precise alignment of the tool with the surface to be grooved. A lanyard with keeper looped through the body secures the instrument to the inspector’s wrist. The entire unit is designed for convenience and completeness in field inspection tasks.
Two cutting tip holders are available.
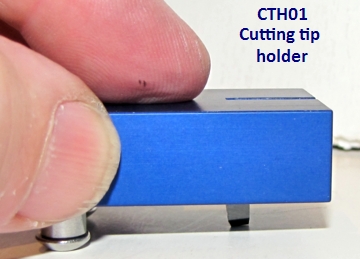
Operation
A special cutting tool (the cutting tip) that is integral to the gauge is used to incise a small precision V-groove through the paint film and into the substrate.
when incising the V-groove with the anodized OG212 Tooke Gage
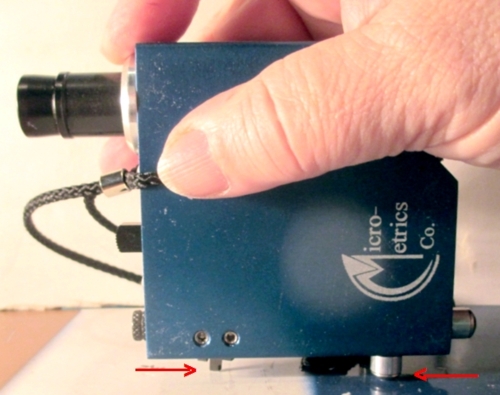
Notice the closer guide stud is not touching the surface.
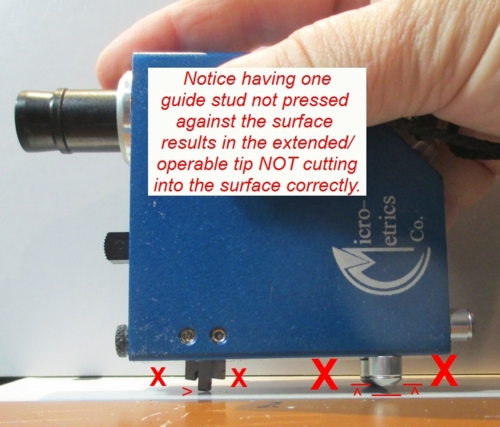
Tooke Gage cutting tips are precision-ground from tungsten-carbide blanks.

The gauge in standard configuration mounts 1X, 2X, and 10X cutting tips. (An optional 5X tip is available.) The gauge can be ordered in any desired configuration, such as with three tips of the same size. You may also order (for a lower price) a gauge with only a single cutting tip and two blank tips (spacers).
Diagram of cutting tip incisions
tip arrangement (in the anodized body)
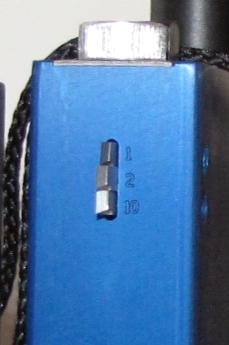
mounted in a (very) old-style gauge body
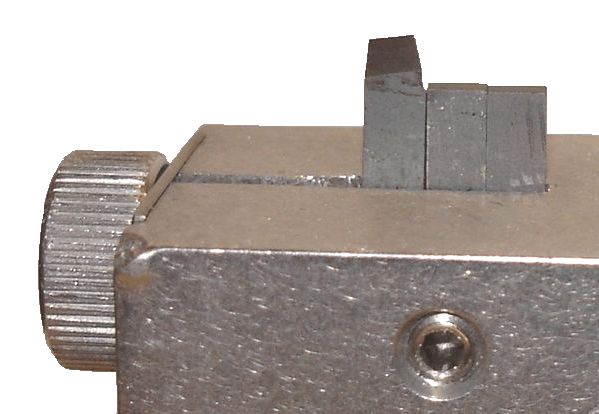
Principle: using the Dual-Measure microscope
Measurement with a Tooke Gage is a function of
the cutting tip face-angle and NOT of the microscope.
One of the best things about the new Dual-Measure scopes is the return to an easy calculation system related to the cutting tip face-angle. As described in the measuring demo, and shown in the drawings in the Geometry section, below, count the hashmarks spaces for each layer of coating, and then calculate the coating depth using the the Dual-Measure scope conversion shown below.
Conversion for the Dual-Measure scope | ||
Cutting tip used: | Face ratio | Each counted hash measures: |
1✕ | 1 : 1 | 1 mil |
2✕ | 1 : 2 | 1/2 mil |
10✕ | 1 : 10 | 1/10 mil |
View through the new Dual-Measure reticle:
the metric scale is marked in 20µm per hashmark.
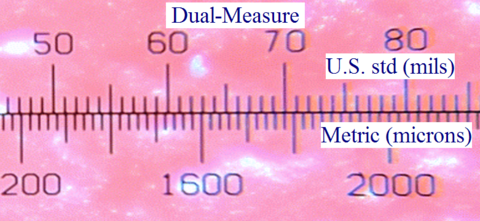
The discontinued universal microscope reticle is marked in 50µm per hash.
For universal scope conversions, see the Reticles section below.
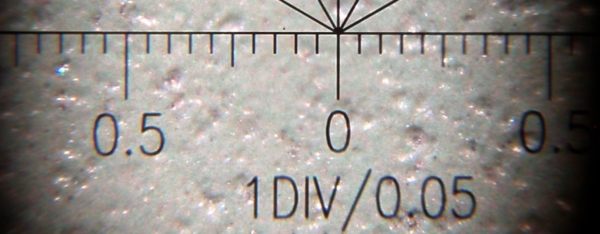
The geometry of the Tooke Gage incision
The easiest example of the process is demonstrated using the 1✕ cutting tip. In essence, you are cutting a triangle into your coating by incising the hypotenuse of a right-angle triangle. With the 45° precision-ground face of the 1✕ tip, you’re cutting an equi-lateral triangle: 1✕ tip has a 1 : 1 ratio. (See the 1✕ tip drawing below.) That is, by counting the hashmarks that define the horizontal triangle-side at the “bottom” of the triangle (and your view through the microscope), you are measuring across the ‘cut-width.’ The 1:1 ratio means your cut-width equals that is your coating depth. With the 10✕ tip, you’re drawing a right-angle triangle, and one-tenth (1/10) the number of hashmarks across the cut-width is your coating depth. (See 10✕ figure below.)
ratio of cut-width : coating-depth
![]() A′ : A = 1 : 1 (no division) |
![]() A′ : A = 1 : 0.5 (divide by 2) |
![]() A′ : A = 1 : 0.2 (divide by 5) |
![]() A′ : A = 1 : 0.1 |
A detailed explanation of the geometry of the Tooke Gage called “Measuring: the Geometry of the Tooke Gage” ![]() |
An interim measuring demonstration
This demonstration, using pictures through the no-longer available “universal” scope shows the process. A demonstration using the Dual-Measure reticle will be posted soon.
Note that in the photo below, the zero-line of the reticle is not lined up for the actual measurement (nor does it need to be; any hashmark will do). The gray/silver-colored “line” is the metal substrate; the white “line” is the (inside of the) green coating, which is what is measured visually through the scope. (See below for a different annotated version.) The cutting tip “draws” the (specifically-angled, depending on the chosen tip face) incision, which allows for calculation of the coating thickness. In this photo, the black marker has not been used to make the edge (top) of the green coating more easily seen.
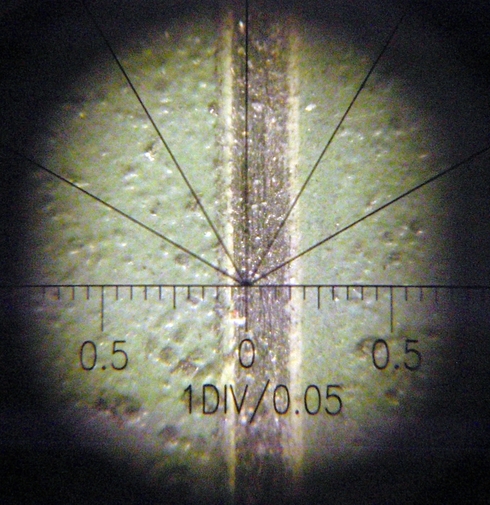
In the next photo, the “zero-line” of the reticle is not lined up with the edge of the primer coating (the white line to the left of the zero-line); it is approximately centered in the substrate (gray/silver line). (This was not intentional; lining up the camera moved the gauge slightly.* Nor does it need to be lined up; any hashmark will do.) “Line A” is on the edge between the substrate and the beginning of the primer-coating: begin your measurement there. “Line B” marks the top of the primer coating/beginning of the top coating (light blue). “Line C” is the incision into the top coating, made easier to see by using the black marker provided with the Tooke Gage. (* The next major Micro-Metrics project after the Dual-Measure scopes is a camera adapter! Stay tuned!)
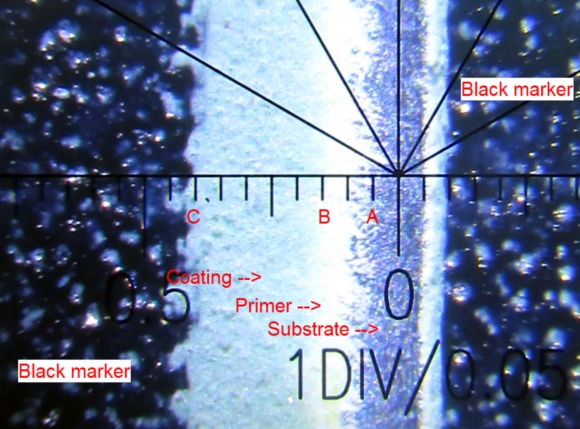
Thus, in this photo and using the discontinued “universal”
scope with 50µm per hashmark space,
the thickness measured for each tip equals:
1 X tip
- “white primer” = 2 reticle/hashmark spaces = 100µm
- “blue topcoat” = 5 reticle/hashmark spaces = 250µm
2X tip
- “white primer” = 2 reticle/hashmark spaces = 50µm
- “blue topcoat” = 5 reticle/hashmark spaces = 125µm
10X tip
- “white primer” = 2 reticle/hashmark spaces = 10µm
- “blue topcoat” = 5 reticle/hashmark spaces = 25µm
(If you have an older gauge, with an English-only or metric-only reticle, please see this page for the measurements that would apply to this incision. These old-style scopes have a green-anodized barrel.) The old-style scope is no longer available) More information about this gauge is posted at that link.
Replacement tungsten-carbide cutting tips.
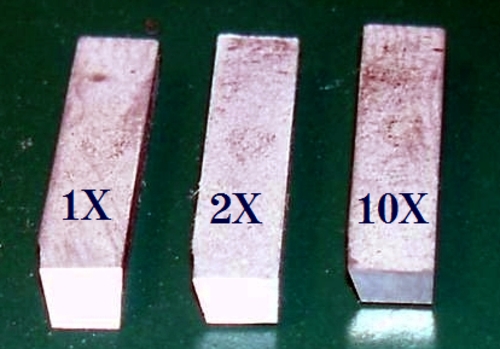
Available in 1✕ (45°), 2✕ (26° 6′) and 10✕ (5° 7′) configurations. An optional 5✕ tip (11° 18′) and blank unfaced tips are also available. (The blank tips provides lateral stability for the operable tip, if only one faced tip is used.)
Shipping specifications
The machined aluminum Tooke Gage comes ready for use in a polycarbonate plastic carry case with two spare batteries, a spare LED bulb, a indelible marking pen, a hex wrench, and a technical data sheet.
- Standard cutting tip configuration is 1X, 2X, and 10X.
- An optional 5X cutting tip is available.
- Any configuration of tips may be requested (for example, three 10X tips; or a 1X, 2X, and 5X).
- You may also order (for a lower price) a gauge with only a single cutting tip and two blank tips (spacers).
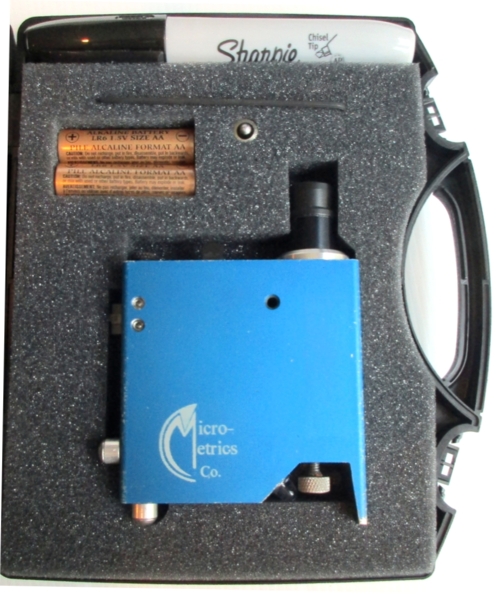
Material: | Machined anodized aluminum body |
Overall dimensions: | 4.5" x 3.5" x1" 11.4cm x 8.9cm x 2.5cm |
Microscope: | 50-power, 45-degree, illuminated with Dual-Measure reticle |
Power | Two 15V AA drycells in the gauge, plus two spares |
Lamp | LED 222 bulb plus a spare bulb |
Cutting tips: | Precision-ground tungsten-carbide cutting tips: 1X, 2X, and 10X (or as desired) |
Shipping Weight: | ~2 pounds (0.9 kg) |
Documentation
- The Technical Data Sheet for the OG212 Tooke Gage is available to be printed on 8-1/2-by-11-inch and A4-sized paper.
- A detailed explanation of the geometry of the Tooke Gage called “
Measuring: the Geometry of the Tooke Gage”
is available.
In the American coatings industry, the word gauge is usually spelled “gage.” Because the Tooke Gage is – and always
has been – known by this spelling, I have used that spelling in the proper name of the gauge, but not elsewhere.