Well-so, more good news and bad news. (Well, bad news followed by hopeful news, followed by putative good news!)
Short version:
I spent Monday driving (6 hr each way!) down to Brunswick GA (out on the South Georgia coast) to meet with the sourcing company president and the engineer I’ve been working with about the benighted new enhanced scopes. The first samples from the second factory arrived last Monday and were not acceptable at all. ({sigh} Just how hard CAN it be to make an exact duplicate of a scope?!)
First face-to-face meeting for us-all, and it was a good meeting. We went over everything. The sourcing co. is going to go back to the second factory to see if they can make the scopes right AND to the first factory (to see if they can fix the mechanical problem that made us drop them).
Loooong drive home, and Tuesday morning, (sourcing co. engineer) Charlie calls and says he was disassembling the (new, second-factory) scopes to make sure he knew everything that needed to be addressed, and he found that one part of the top optics (in the eyepiece) had been **screwed in up-side-down**! When he reversed that piece, the new-new scopes worked perfectly. He is sending me one again to test and, we hope, approve. (Because I won’t accept ANYthing I have not actually had in my hands to test!)
So, I once again have hope we might actually GET there! “There” being actual great working scopes to replace those mostly undesirable “universal” scopes! (Cock-eyed optimist or am I being reasonable? Only time will tell!)
version, without tooling up for it. Shown next to their final version.
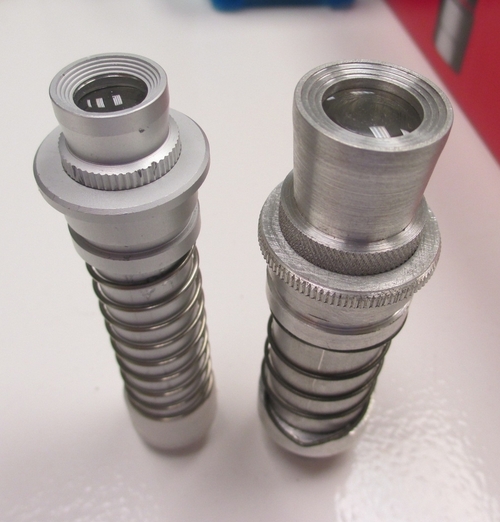
Longer version:
In our last installment, you may remember that last August we fired the first (and, to that point, only) microscope factory after a continuing “Keystone-cop cascade” (am I the only one old enough to remember who they were?) of mistakes, flaws, and less-than-optimal choices (not ours, theirs!).
The sourcing co. found a new factory that promised great new sample-scopes would be supplied within 30 days of … you know … last AUGUST?! The first samples arrived in late December. Engineer Charlie called and said he was just going to send them straight back to China, because the samples couldn’t even focus on the surface the gauge was standing on. ({sigh} I said: let me come down there and we’ll go over everything.)
I had emailed to the SBDC fellow who referred me (in April 2012!) that I didn’t know if I was going down there to fire the sourcing co. president, or he was going to fire me, or we were going to find a way to make this process work! (Turns out: the third…)
We went over all the previous prototypes and the drawings and the gauges and the problems and the successes. End result: They are going back to both the second and first factories (the first one did the optics perfectly — but there was an insuperable mechanical problem (with their “final production” run!). The disqualifying problem was a mechanical flaw: the bottom collar was not made smooth-and-flush (see previous blog entry for pix), and so the focusing screw would hang up and prevent the scope from focusing without backing-out the focusing screw, raising the scope by hand, and then continuing with the focusing screw. But they had the optics right!
The second factory? Pretty scopes, worked well in the gauge bodies: but could NOT focus on the surface the gauge was standing on.
Tuesday morning, Charlie calls and says he was disassembling the second-factory scopes to make sure he knew everything that needed to be addressed, and he found that one part of the top optics (in the eyepiece) had been **screwed in up-side-down**! When he reversed that piece, the new-new scopes worked perfectly. He is sending me one again to test and, we hope, approve. (Because I won’t accept ANYthing I have not actually had in my hands to test!)
I stressed that I need them to make sure there was some ‘physical’ way for a future-assembler to know which way is up on this piece. Five years down the track, could be some new guy at the factory, maybe new guys at the sourcing co., and I needed to make ABSOLUTELY SURE they wouldn’t be putting the eyepiece components in up-side-down again. I don’t care if it’s a notch or a stamped-on arrow, or they make one side a half-inch longer (it’s inside the barrel — no effect on the focus): there has to be a(s close as possible to a) “sailor-proof” way to assemble these things.
(I described for Charlie the old P-250 pump in the Navy (here’s a version: http://my.firefighternation.com/forum/topics/889755:Topic:2096360) — it has NO moving parts, not one! And yet (granted, rarely), sailors STILL sometimes manage to break it! So I want to make this assembly process as close to “sailor-proof” as we can! “THIS SIDE UP!” eh?)
So, I once again have hope we might actually be on track to finally (three years and at least ten months down the track!) have the new enhanced microscopes.