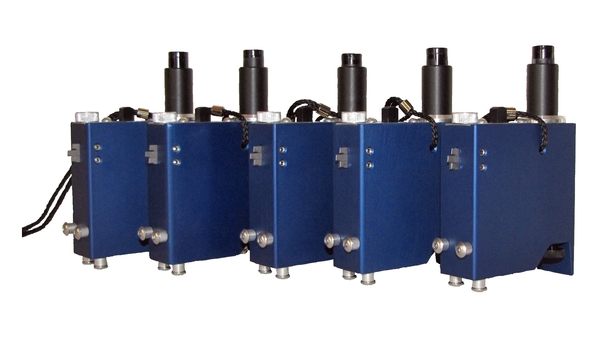
As part of the upgrading of the OG202 metal-bodied Tooke gauges, going forward, the OG202s will be anodized. Aluminium alloys are anodized to increase corrosion resistance and increase surface wear resistance . The anodic layer is non-conductive. Anodizing will protect the aluminum parts by making the surface much harder than natural aluminum. Aluminum oxide is grown out of the surface during anodizing and then becomes aluminum hydrate, which is extremely hard. The porous nature of the anodized layer allows the product to be dyed. Type II anodizing gives an anodized layer of 0.0002″to 0.001″.
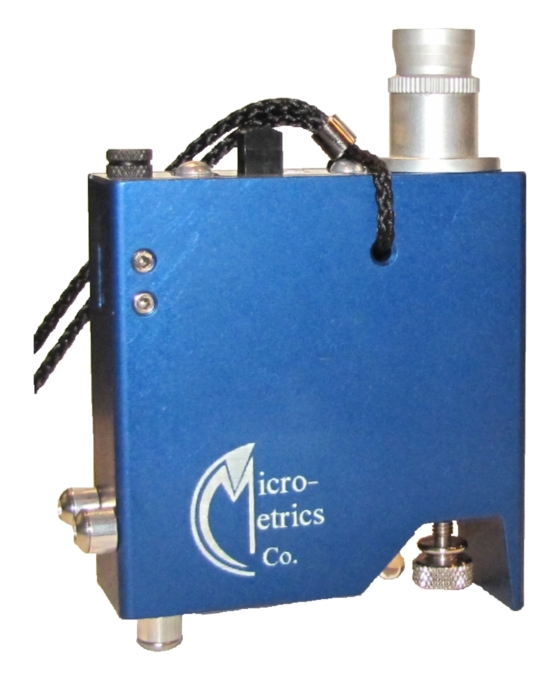
The following text is modified from the Aluminum Anodizers Council http://www.anodizing.org/Anodizing/benefits.html:
Anodizing’s Benefits
Durability. Most anodized products have an extremely long life span. Anodizing is a reacted finish that is integrated with the underlying aluminum for total bonding and unmatched adhesion.
Color Stability. Exterior anodic coatings provide good stability to ultraviolet rays and do not chip or peel.
Ease of Maintenance. Scars and wear from fabrication, handling, installation, frequent surface dirt cleaning and usage are virtually non-existent. Rinsing or mild soap and water cleaning usually will restore an anodized surface to its original appearance. Mild abrasive cleaners can be used for more difficult deposits.
Aesthetics. Anodizing offers color alternatives and unlike other finishes, anodizing allows the aluminum to maintain its metallic appearance.
Health and Safety. Anodizing is a safe process that is not harmful to human health. An anodized finish is chemically stable, will not decompose; is non-toxic; and is heat-resistant to the melting point of aluminum (1,221 degrees F.)
Since the anodizing process is a reinforcement of a naturally occurring oxide process, it is non-hazardous and produces no harmful or dangerous by-products.
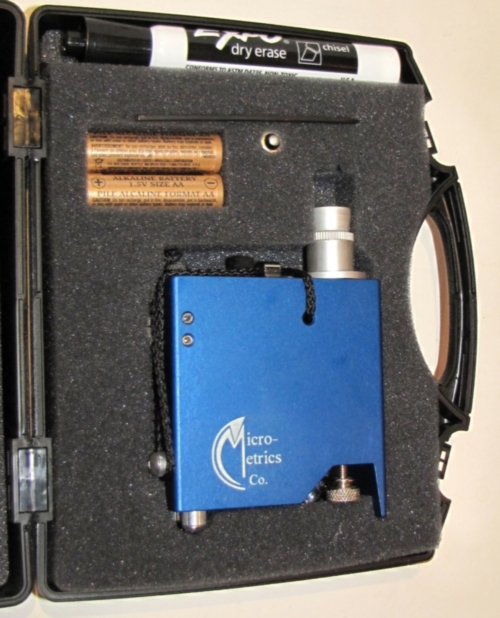